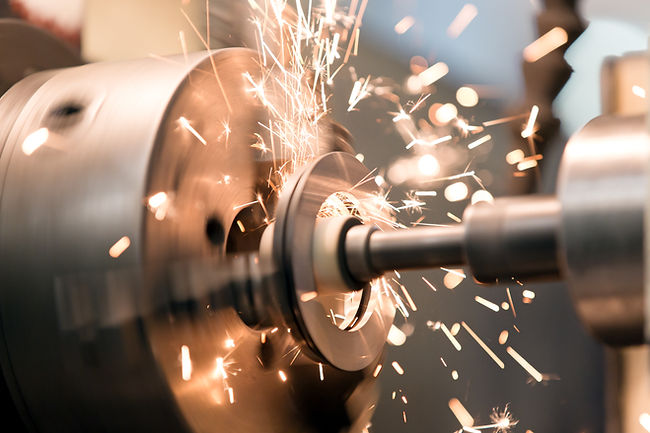
PRODUCTION PROCESSES
MOLD MAKING
Mold making is also referred to as pattern making and is a skilled trade that incorporates elements of fine woodworking. Although our design engineers help to design the mold, it is customarily a pattern maker who executes the design. Typical materials used for mold making are wood, metal or plastics. A mold is a replica of the final product that needs to be manufactured. The pattern is used to prepare the mold which represents the cavity into which glass fibers and polyester resins are laid for lamination. Often, molds are repeatedly cast from themselves to produce male and female versions until the desired strength and finish of the final mold is achieved. The process however begins with patterns that are made to exacting standards of construction and dimensions.
NOD offers a full CAM service so that all of our designs can be taken through to finished product on our state of the art CNC machine. This allows us to offer our customers a complete package from an experienced, well established, reliable company.
For freeform surfaces we usually make the molds by using Robot machine with 5 or 6 axes outsourced .In our references pages you can find some photos of mold samples which had been produced accurately.
SPRAY UP LAMINATING
The Spray Lay-up technique is an open-mold laminating of GRP as it is a semi-automated process, requiring a different manual skill set. It utilizes more expensive equipment.
Especially for architectural GRP pieces or panels we use the spray-up process for production. This process is differs from the hand lay-up method in the way the materials are applied to the mold. The desired “finished side” of the part dictates the orientation of the mold. In starting the manufacturing process, the mold is cleaned and prepped with a release agent. If a cosmetic surface finish is required, the mold surface is covered with a gel coat and allowed time to cure. Spray up utilizes a chopper gun which sprays catalyzed resin and chopped glass fibers simultaneously. The multi-end roving is fed to the chopper gun from a creel that contains several thousand feet of gun roving. This multi-end roving is cut or chopped by the action of the spray gun into strands ½ inch (12mm) to 1 ½ inches (36mm) in length and combined with a spray of resin immediately in front of the gun nozzle. The saturated glass/resin matrix is then deposited on the mold surface. Multiple passes build the laminate to the specified thickness. Due to the random orientation of the chopped fiber, the part is easily formed and provides outstanding structural integrity. As in the hand lay-up process, consolidation by hand rolling is required to compact the laminate and remove entrapped air. Also as with hand lay-up, the ratio of glass fiber to resin is critical.. Spray up process supports higher volume part programs and it is faster than hand lay up.
NOD uses CE branded machines which are especially designed for spray up processes.
CURING
After spraying fiber and resin to required thickness, GRP units shall be adequately cured in accordance with the resin manufacturer’s recommendations Curing of the product is done either at room temperature or at elevated temperature. We care to ensure that units are not distorted while being cured.
In our production area; we use individual telescopic tents and portable heaters that provide hot air to these tents to reach the appropriate temperature with telescopic control tents, if the room temperature is not suitable for curing.
PAINTING
NOD provides a common Class A, high-gloss, gel coat surface finish to many of its customers. As paint-ready surfaces have become the norm, NOD offers variations of two basic finishes; a sanded gel-coat finish painted, or an A-Class painted top-coat flat finish. Several variety of sanded textures and colors are available on multiple surfaces of GRP products. Faded, scratched or lightly damaged surfaces may be improved or repaired using a suitable brush or spray-applied coating.
NOD uses JOTUN Jotashield Tex Ultra for its surface finishing; which is a superior quality, flexible, water based paint based on pure acrylic emulsion. Jotashield offers very good weather and water resistance which acts as anticarbonating coating. It comes also with an A-Class reaction to fire.
TRANSPORT PREPARATION
There is no technical limit to the size of a GRP composites part, although size may be limited by transportation and installation constraints. As with traditional materials, project-specific tolerances must be considered when designing GRP composites parts. Installation considerations should be discussed when selecting the optimum size of a GRP composites part.
Impact, excessive distortion, premature handling, or unanticipated or excessive shipping loads can compromise the GRP composite part and its finish. NOD always gives attention to the following:
- The means of lifting and handling GRP products are assessed during the product design phase. At times, lifting points, harnesses, or other means are engineered and installed in the composite parts to ensure their safe handling.
-Our shop drawings include recommended handling procedures as well as the center of gravity for large components and/or non-typical geometries, and also
- We take care to ensure that the finish of the shipped GRP part is not damaged or blemished due to wrapping or handling prior to adequate finish curing.
-GRP components should be lifted and not dragged, rolled, dropped, or thrown.
- Open-end parts such as cylinders and partially-hollow objects may require internal or external bracing during handling and installation to prevent damage in transit.
- GRP components can become damaged from excessive tie-down forces. Tie-down forces should be spread over a sufficient area to prevent part crushing, and applied to supporting framework, connections, or other approved locations to prevent part damage, excessive deflection, or movement during transit.
NOD makes the needed designs and calculations of on-board equipment for transportation vehicles, to provide suitable and safety loading and unloading process.